数字孪生:企业数字化转型的支点
北京呼风唤雨文化传媒有限公司
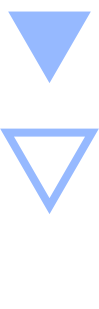
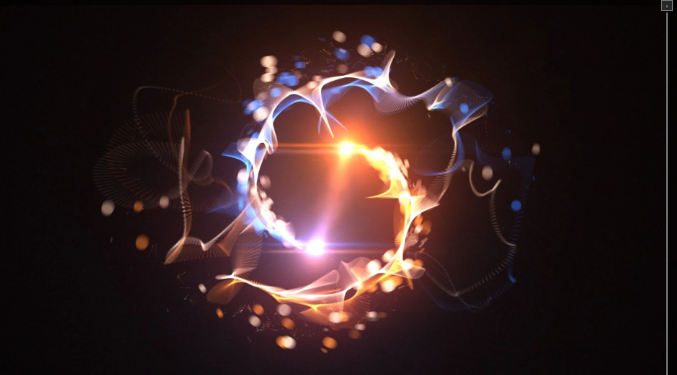

数字孪生:企业数字化转型的支点
文 | 龙小昂
随着物联网、大数据、人工智能等技术的发展,新一代信息技术与制造业正在深度融合,人们与物理世界的交互方式正在发生转折性的变化。数字化转型,正在成为企业的重要战略,而数字孪生,则成为全新焦点。本文通过对数字孪生在工厂中的实际应用,为企业数字化转型提供了一套落地可行的方法。
工业企业的数字化转型,需要面临制造理念、组织方式和商业模式的多种变革。一个产品,从设计理念开始,经历了制造、使用和报废,跨越了时空,呈现出一个完整的生命周期。如果设想这种产品有一本履历表,那么它将忠实地记录了这个产品的各阶段生命周期相关的数据。各种健康状况和风险,都会一目了然,然而事实却并非如此。对于制造商而言,各阶段的数据通常呈现孤立、分散的特征,尤其是用户对于产品使用过程中,基本就是黑匣子。数据的分裂,让产品的各个阶段,都成为一座座孤岛而互不相连,数据失去了流动性,大大约束了人们的洞察力。
数字孪生,作为连接实体与数字空间的一种高保真、实时互动的可视化模型,随着工业互联网的发展,成为一种全新而有效的解决方案。工厂的设备,可以通过实时可视化的数字孪生,模拟机器在生产系统中的表现,通过虚实交互、数物融合和知识自动化,形成一线操作者和管理者的决策支撑系统,提供更加实时、高效、智能的服务[1]。
企业数字化转型,围绕着数据驱动而来。而数据要真正产生的价值,需要靠企业知识体系来提供。因此,数字化转型,首先需要面对的是企业知识的梳理。但是传统的知识体系,往往呈现非常僵化的状态。例如,工程图档往往是企业的重要知识资产,但很多制造企业都是采用传统的图纸档案管理方式,以“底图”或“蓝图”的形式,进行分类、分密级归档保存。而代表企业重要的知识体系,如工艺说明、操作手册、工程文件等,已经随着企业信息化应用的逐步发展,一般都是通过扫描后进行管理。
然而这些图纸、电子文档所保存的知识,都是静态、分散和割裂的。颗粒度太大,缺乏语义的连接,无法实现相互之间的关联,流动性很差。这种知识体系,只是被收藏起来,但却无法高效重复使用。对于资深工程师而言,这只是一种储存方式而已,因为信息查找而言,仍然非常低效;而对于经验不足的员工而言,这些知识则像是被隐藏起来。
面临数字化转型,由于缺乏系统性的知识体系支撑,因此工业企业呈现出如下的困境:
1)工业场景复杂,存在海量多源异构的工业数据,多样性、复杂性的工业数据,造成工业场景信息孤岛化,数据利用价值低。
2)工业场景中,存在显性知识与隐性知识,各种结构化、半结构化和非结构化知识,知识关联性弱。
3)人工智能(AI)正在逐渐成为大数据分析的重要技术,但是传统AI训练,过度依赖人工开发算法。它无法关联自然语言所对应的概念、属性、关联性等。
4)随着工业数字化普及,海量的CAD、CAE文件以及数字化的各类文档、说明书、操作手册等,信息量暴增,给用户决策带来新的痛点。
5)工业知识专业性强,且涉及技术领域广。零散化的知识晦涩难懂,工业术语解释专业性强,经验知识传播、传承困难。
而通过知识图谱,可以将各种概念,通过编码连接的方式,形成语义连接,将隐形的知识显性化;而数字孪生技术,则可以在传统静态模型中,增加了实时运行数据的反馈,动态记录,并且用可视化的方式进行展现。这将彻底改变原有的知识管理方式,激活沉默的知识资产,从而帮助人们重新认识、管理和控制机器世界。
构建机器数字孪生,不仅仅是信息组织和表现形式的图形化,更在于构建过程中,是将企业的知识体系贯穿其中,信息上下游之间的背景链路清晰明了。而在构建数字孪生的过程中,可以采用“双模数字孪生”的方式,就是将几何模型和和机理模型相互嵌套。结合不同的设计、制造和运维的阶段,知识体系嵌入其中,最终在使用的时候,就可以实现知识自动化。
构建物理几何模型,首先是从零配件开始。例如,一台烟草包装机,有1.5万个零件,需要一一建模,并且建立设备零部件库。这些零部件库的最小单位为零件级别,如螺丝、螺母。主要数据获取方式,包括从CAD软件、数据表以及现场测绘开始,构建实体等比的数字化模型。
机理模型,就是要将几何空间的零部件,跟控制系统的机器动作进行匹配。机器的真实运动轨迹,在几何模型都有对应描述作。这其中,都是通过数据标签,来标识零部件的状态,并且跟控制逻辑相对应。例如,薄膜纸会剔除那些无法包装的烟支和烟包。而烟支无法包装的原因会有几十种:薄膜褶皱、烟支重量不够、圆周不够圆、空投、漏气、重量等。需要深入了解这些机理,然后将其做成模型和算法,并与几何模型相对应。
第一种是设计类。要设备的设计资料出发,运用数字孪生技术,全面刻画设备的物理属性,实现虚拟设备对物理设备的真实映射,最终完成对物理设备的完全镜像。
第二类是制造知识模型的构建。运用数字孪生技术全面的刻画设备与产品之间的属性,实现虚拟设备与物理设备的数字模型真实映射。制造阶段所涉及的知识按其特性可分为三类:
(1)基础知识:为装备制造企业核心数据,企业组织结构、岗位、工种、人员、存货档案、固资编码、供应商等信息。
(2)生产管理知识:如生产计划、产品指标、原材料清单、绩效考核指标等。
(3)设备知识:如供应商、规格型号、操作说明、操作规程等。
第三类是运维知识模型的构建。基于设备服务知识模型,在采集的实时数据、历史数据及领域知识等,共同实现设备的多维数字孪生模型构建。建立各种故障代码、维修对策库,并且提前通过虚拟模型,进行仿真验证,从而实现对机器状态检测、故障预测以及维修策略建议等功能。
以上三种知识模型的建立,都离不开一套表达各种物品之间关系的知识图谱,这是构建在行业规则之上的编码体系,具有很强的支撑作用,能够快速建立知识模型,并且用可视化的方式,将背后的知识体系表达出来。
在知识体系的基础上,构建了高保真的数字孪生,就可以在现场,提高员工的判断力,从而提升工厂的运营效率。
机器作为工业生产的必备工具,可视化管理是工业数字化转型必经阶段。而数字孪生,则更胜一筹,不仅仅让使用者对设备有形象具体的图形理解,对设备现实的状况及所有参数数据等信息一目了然,而且以非常体系化的方式,引导用户轻松使用机器。
设备数字孪生,可以将一台机器以3D的形式,展示设备整机、部套、零件之间的层次关系。用户可以借助于导航树,在烟机的不同零部件之间进行自由切换,深度了解。数字孪生会呈现出拆分动画,逐级递进,用户可以直接与场景中的3D对象进行交互,用层层“爆炸图”的方式,查看机械零件、子部件的详细信息。
图1:机械结构层层分解图
设备的元器件、油路、气路等,都是等比例建模,携带各种属性信息。设备数字孪生,就像为操作者提供了一台CT机,看到机器的各种结构和属性,从而对机器有着深刻的了解。
基于数字孪生技术创造出来的3D互动模拟的在线培训系统,可以实现现实与虚拟仿真的统一。它突破了“分别翻看图纸说明书“的传统培训模式的限制,而是直接“在线手把手”。各种不同的操作规范、说明手册等,都被统一集成到一个界面上,每一步行动都有说明和提示。在大大缩短培训周期的同时,丰富了培训内容,并减少了现场实训的成本损耗和危险性。以前一台进口的高端烟草机械,即使是成熟的工人,完全掌握一台机器,需要用两三年。而现在生手工人,只需要3-6个月就可以完全上手,大大减少了对熟练工人的依赖性。
图2:虚拟专家引导操作培训
传统设备管理工作中,设备监管、设备控制、设备维护、库存管理等各个业务模块之间数据不互通互联,存在信息孤岛。同时还存在设备管理效率较低、设备维护成本高等问题。而基于数字孪生的设备管理应用,能够让现场发生故障的时候,不仅仅是知其然,而且知其所以然。
例如机器如果发生停机故障,传统方式需要统治维修人员,然后去现场排查,排查往往又需要半天时间,找到故障原因。机器非计划停产,会给企业带来很大的损失。但这种现象,在车间里非常普遍。
而通过机器数字孪生,就可以在车间的任何一台人机界面上,直接就可以看到什么位置、何种部件、发生了何种故障。如图3中所示意。
图3:设备数字孪生自动完成故障报警及诊断
这种基于设备服务知识模型,能够对设备状态进行评估,准确预警,从而帮助优化设备检测、维修计划安排和人力资源分配,大大提高了设备的运行效率与可靠度。
这种应用,也可以在云平台上,对多个系统实时远程管理,并且可以细化到产线级、设备级、零部件级的运行状态,了解设备故障问题严重程度、故障描述、处理方法等
而下一步,设备数字孪生将进一步推动智能机器的进化,实现自适应的机器控制。根据故障情况,可以直接反向去控制机器。
从图纸到零件,从制造商到最终客户,从决策者到管理者再到操作者,数字孪生的应用贯穿在整个设备的全生命周期之中。而知识作为指导人和机器学习及做事的指令集合和规则体系[4],为高保真、实时互动的数字孪生提供了核心支撑。通过数字孪生技术,实现工业知识模型化、模型软件化、软件云端协同化,推动业务流程与机器效率的提升,真正实现了知识自动化。
实际上,数字孪生的应用并不限于机器,往上它还有车间级、企业级和城市级。不同层次的数字孪生,对应不同的决策判断,从而使得数字化转型可以逐层切入。高保真、实时交互的数字化孪生,成为数字化转型的重要支点。
[1]刘高升.知识自动化助力产品全生命周期管理.《清华管理评论》2020年11月刊
[2]陈冬生.基于产品全寿命周期的航空制造企业质量知识管理初探.经济师,2021年第2期:34
[3]陶飞,张贺,戚庆,林张萌,刘蔚然,程江峰,马昕,张连超,薛瑞娟.数字孪生十问:分析与思考.计算机集成制造系统,2020年第1期:1-17
[4]射手盼盼,恒信知识库建设方案说明书,百度文库,2018年06月28日:01-0
[5]刘绪忠,宋春咏,孙磊,马法雷.基于知识图谱的故障智能诊断手段研究.山东通信技术,第39卷第2期2019年6月:19
[6]李浩,陶飞,王昊琪,宋文燕,张在房,樊蓓蓓,武春龙,李玉鹏,李琳利,文笑雨,张新生,罗国富.基于数字孪生的复杂产品设计制造一体化开发框架与关键技术.计算机集成制造系统,第25卷第6期2019年6月:1321-1336
[7]张长信.数字孪生体在产品生命周期管理中的应用探究.科技风,2019年3月:13-14
作者介绍
龙小昂
深圳华龙讯达信息技术股份有限公司CEO,全国信息化和工业化融合管理标准化委员会专家委员、中国工业互联网研究院工业互联网推进委员会专家委员、深圳市工业互联网专家委员会专家。
拥有多年自动化控制和信息化管理的研究和实践经验,运用数字孪生技术在制造企业的应用和发展有深刻领悟和研究。带领团队自主研发数据采集、数字孪生、工业物联网和工业互联网等前沿技术,获得170多项专利及软件著作权。
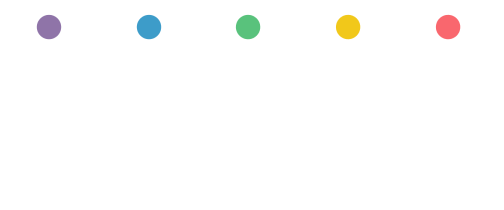
本文系《卫星与网络》原创,转载及引用部分观点至微信公众号或其它新媒体平台、及网站,请在文首注明出处、公众号ID及作者。感谢支持有态度的媒体!
未按照规范转载及引用者,《卫星与网络》保留追究相应责任的权利
部分图片难以找到原始出处,故文中未加以标注,如若侵犯了您的权益,请第一时间联系我们。
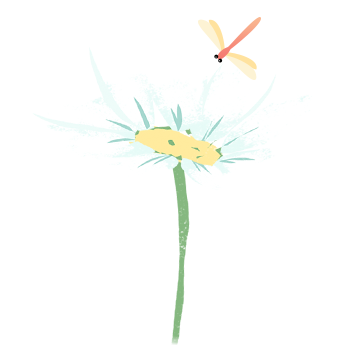
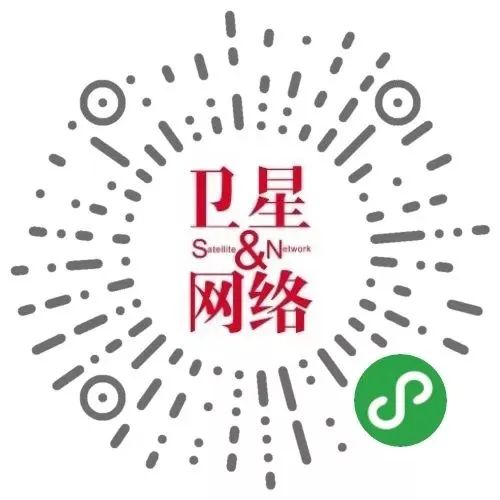
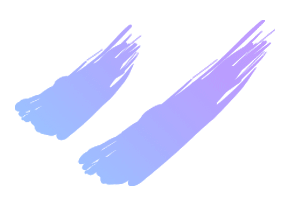
电子杂志,扫码阅读
期期精彩,不容错过
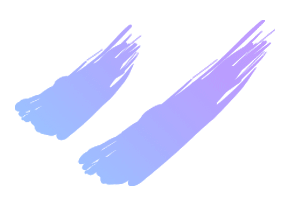
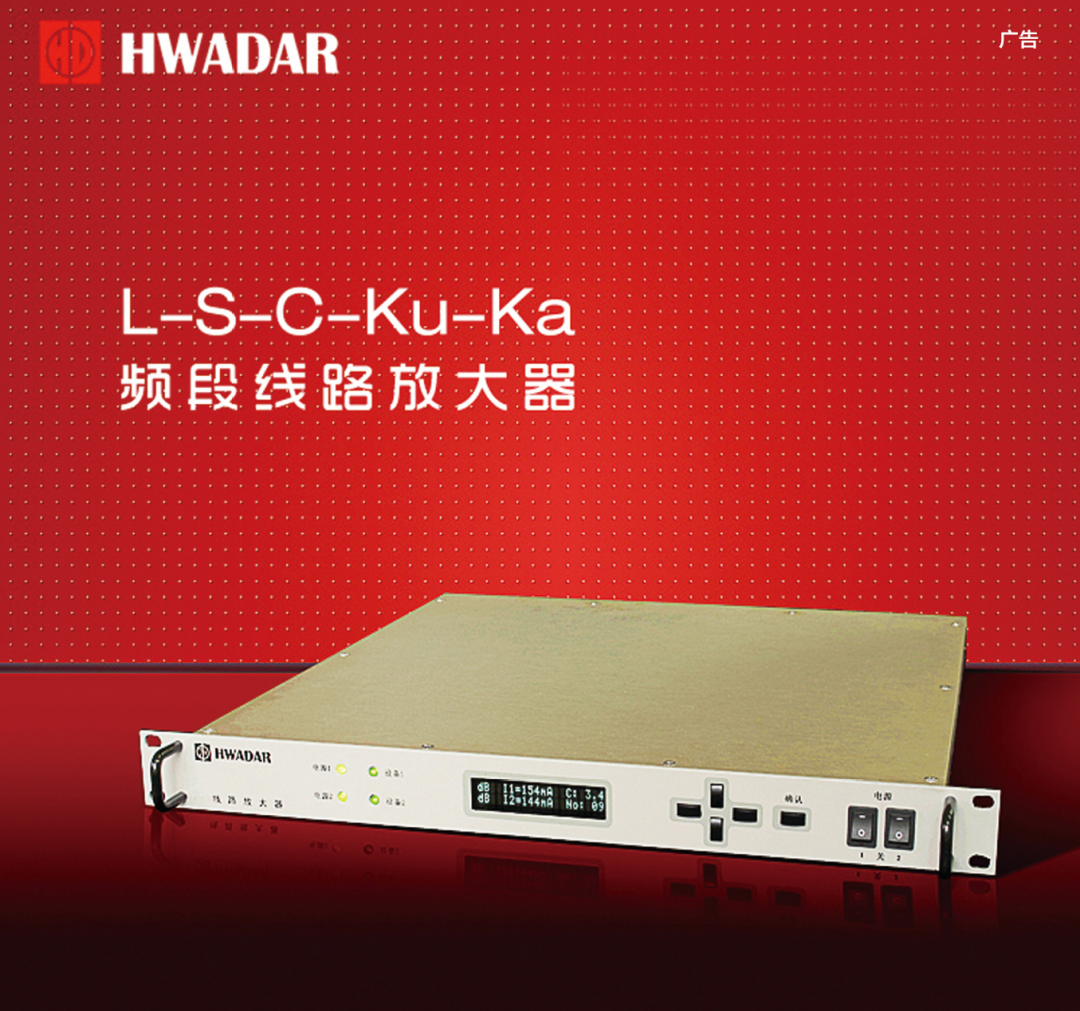
· 卫星与网络微信公众号(ID:satnetdy)团队
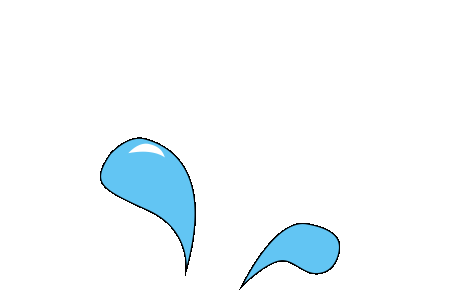
