为什么说机器视觉是实现工业4.0的关键?
物联网智库 原创
转载请注明来源和出处

导 读
机器视觉是赋予工业机器人智慧化,并助力整个工业从3.0时代步入4.0时代的关键一环,为智能制造的落地打开了“新窗口”。
早在十几二十年前,随便走进一家电子厂,人们会看到一排排工人正在进行装配、贴标或质检等重复性的劳动作业。这是工业1.0、2.0时代司空见惯的场景。
沧海桑田,如今,在许多现代化工厂,工人变成了流水线旁负责巡检的“配角”,工业机器人替代了繁重的人工作业,电子信息技术的广泛应用让生产的自动化水平大幅提高,工业界也由此步入了3.0时代。
然而,传统的工业机器人大多是通过示教再现或者预编程来实现各种简单的操作,这极大地限制了机器人的应用。如果能让机器像人一样具有自我意识,可以根据产品的位置、亮度、颜色、表面特征等信息进行对应的操作,显然能进一步解放生产力,完成柔性化的制造,而实现这一切的前提就是为机器人装上“眼睛”,也就是“机器视觉”。
某种意义上可以说,机器视觉是赋予工业机器人智慧化,并助力整个工业从3.0时代步入4.0时代的关键一环,为智能制造的落地打开了“新窗口”。
“神通广大”的机器视觉
顾名思义,机器视觉就是用机器代替人眼来做测量和判断,通过视觉系统对产品图像摄取,同时将被摄取的目标转换为图像信号传送给专用的图像处理系统,得到被摄目标的形态信息,再将像素分布和亮度、颜色等信息转变成数字化信号,图像系统对这些信号进行各种运算来抽取目标的特征,进而根据判别结果来控制现场的设备动作。
和人眼相比,机器视觉具有效率快、精准性高且永不知疲倦等显著优势,因而被广泛应用于工业制造的各个环节,比如上下料过程中使用机器视觉进行定位,引导机械手臂准确抓取;比如在自动化包装领域进行物品数量的识别和数据的追溯;再比如对一些精密度较高的产品进行分类和瑕疵检测,这也是机器视觉目前应用最广泛、取代人工最多的环节。
我们不妨以汽车轮毂分类/分割场景为例:作为轮胎的骨架,轮毂扮演着汽车配件中的重要角色,根据直径、宽度、成型方式、材料不同种类繁多。
从制造的维度来看,汽车轮毂大多是铸件,铸造完成后要进行精加工,轮毂有上百种类型,不同的类型应选择不同加工路线、加工机床、刀具等。在自动化生产线上要实现多品种的混流生产,首先要完成的就是轮毂类型的识别。除此之外,轮毂的质量好坏还直接决定了车辆行驶过程中的安全性能,然而其制造成型过程中受工艺参数、冷却系统等因素的影响,却极易产生气孔、缩孔、缩松等内部缺陷。为了保证产品质量,缺陷检测/分割环节也必不可少。
无论是轮毂分类还是分割,这些任务早期都是由人工方式来完成,流水线周而复始,工人没有片刻休息时间。在工作强度大、时间长、长期紧张的工作状态下,工人容易感到疲倦,在作业中也不可避免地受到情绪波动、注意力不集中、疏忽大意等因素的影响,导致分类/分割工作的速度、稳定性和准确性都无法保障。
不断迭代的机器视觉方案
对症下药,基于上述痛点,越来越多机构开始探索自动化甚至智能化的轮毂分类/分割方案。
自动轮毂检测场景
先来看轮毂分割场景。X射线无损探伤是目前检测轮毂内部缺陷的最佳方式,具体而言,初始成型的毛坯轮毂被机电系统送入铅房后,分区域多次成像,能实现整只轮毂的全部检测。
为了替代传统的手动检测,有的企业采取半自动检测的方式,即提前在下位机设置好轮毂的运行流程,每个部位的成像过程无需人工干预,检测人员仅需观察该部位的X射线图像来决定产品质量;还有企业更进一步,在上位机设置好轮毂缺陷检测的相关参数,整个过程无需人工干预,全部自动完成,而在全自动的检测过程中,轮毂缺陷的自动分割算法起着至关重要的作用。
再来看轮毂分类场景,当前,已经有不少高校提出了基于机器视觉的分类算法。
东北大学提出了一种基于机器视觉的汽车轮毂识别系统,其根据实验选择了五个特征:轮毂中心是否有孔洞,轮毂边缘区域的孔数,轮毂半径,轮毂面积,以及旋转不变性,利用投票分类器对提取的特征进行分类。与传统方法相比能达到较好的效果,缺点是先验信息太多,需要人工选择较明显的特征费时费力,且由于提取到的特征较少,对于结构复杂的轮毂辨识度差,结构相近的轮毂也难以区分。
中北大学提出了一种基于 OpenCV 和 MFC 平台的轮毂分类技术,与传统的识别方法相比节省了时间,但由于形态学处理的破坏,泛化程度较低;南京信息工程大学提出了一种基于统计模型的轮毂分类方法,使用背景去除、形态学处理、局部二值化和边缘提取算子等多种方法进行特征提取,能进一步提高分类精度,但能够成功识别分类的轮毂类型较少且检测方法非常耗时……
通过上述分析我们可以得知,机器视觉解决方案的部署本身是一项非常复杂的工作,涉及许多专业技术,需要很多专业人才,期间会耗费大量成本且涉及大量试错,制造商想要依靠自身开发这样的一套解决方案,可谓难如登天。
让机器视觉不再遥不可及
如何让制造商快速掌握机器学习这项“秘密武器”?英特尔与无锡信捷电气股份有限公司(下称“信捷”)联合推出了一套基于深度学习的轮毂分类/分割解决方案,为轮毂检测行业提供了新的思路。
基于信捷自主研发的新一代机器视觉应用开发平台X-SIGHT VISION STUDIO Pro,制造商无需编写代码,只用在软件中拖拽组件,就能完成开发——这相当于把复杂的专业摄像机直接变成了“傻瓜相机”,大大降低了用户入门的门槛。
X-SIGHT系列产品
除了具备图形化界面、提供快速的应用开发环境,帮助用户快速上手并轻松创建典型应用之外,该平台还提供了强大的图像分析能力,甚至具备自我学习优化能力,是一个不断进化迭代的平台。得益于此,用户能以更高的效率开发定制化的大规模项目,从而缩短研发周期和成本。
X-SIGHT图形用户界面
你可能会疑惑,为什么信捷的平台能够将机器学习“化繁为简”?原来其平台背后,集成了英特尔® OpenVINO™、oneAPI加速方案。这些软件就如同“催化剂”一般,为信捷的方案部署和模型加速提供了更高效的工具。
其中,OpenVINO™ 视觉工具套件是一款面向高性能计算机视觉和深度学习应用的快速开发套件,基于最新一代人工神经网络,包括卷积神经网络 (CNN)、循环网络和基于注意力的网络,可跨英特尔硬件扩展至计算机视觉和非视觉的工作,从而最大限度地提高性能,在边缘到云端都能展现高性能 AI 和深度学习推理部属的加速。这增强了信捷产品的深度学习神经网络推理能力,助力其为客户提供更优的解决方案。oneAPI 则是一种跨行业、开放、基于标准的统一编程库,可提供跨加速架构的通用开发体验,帮助信捷提高应用性能、工作效率和创新能力。
机器视觉场景复杂,英特尔为此开发了诸多工具套件,以满足用户在各类工业场景下的需求,促进更多的机器视觉应用案例落地,为工业机器视觉的发展提供技术支持。
基于信捷和英特尔的这套联合解决方案,制造商能够通过摄像头采集轮毂图像,传输至网络进行识别分类,实现快速、准确、稳定的响应,从而大大降低人力成本,提高生产效率。
结语
以智能制造为主导的工业革命4.0正影响着各行各业,而工业机器视觉将是驱动未来工业数字化、智能化的重要动能,不仅是汽车制造产业链在积极引入机器视觉解决方案,更广泛的工业领域也期望借助该技术实现数字化升级、柔性制造的变革。
往期精选
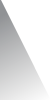
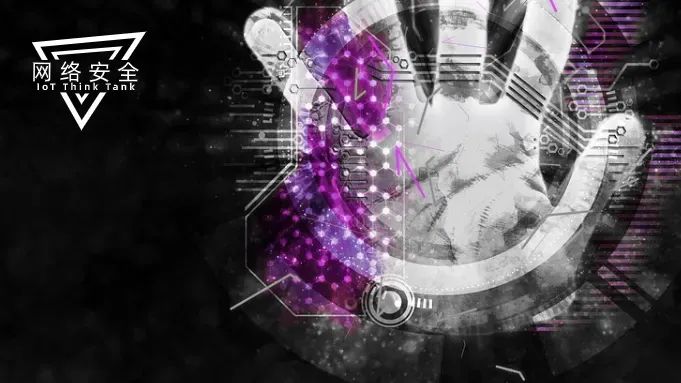
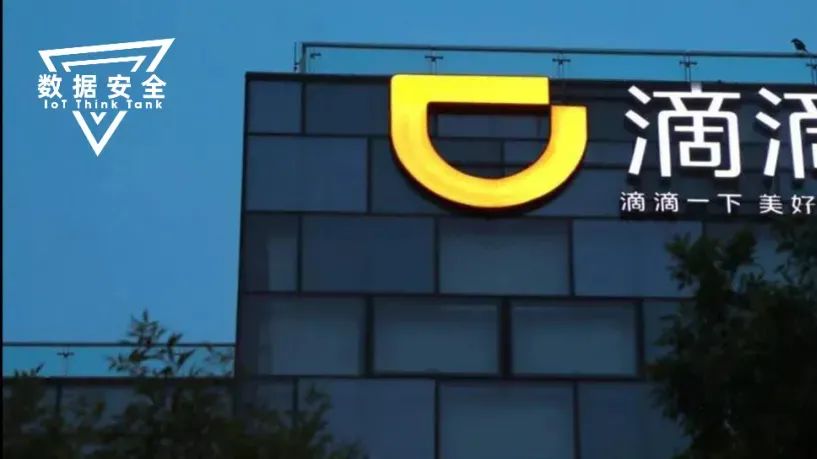
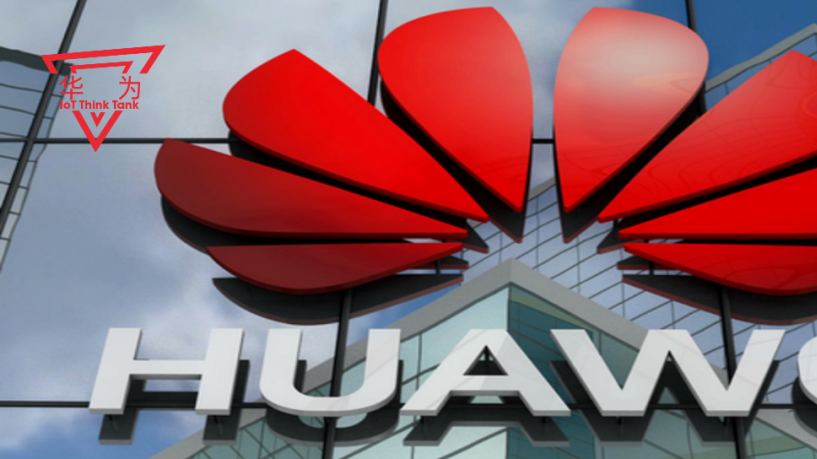
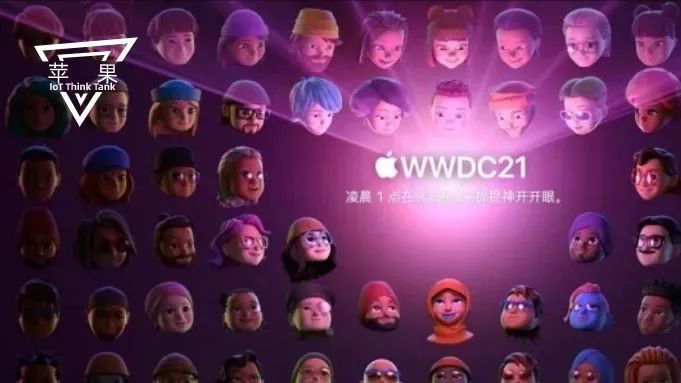
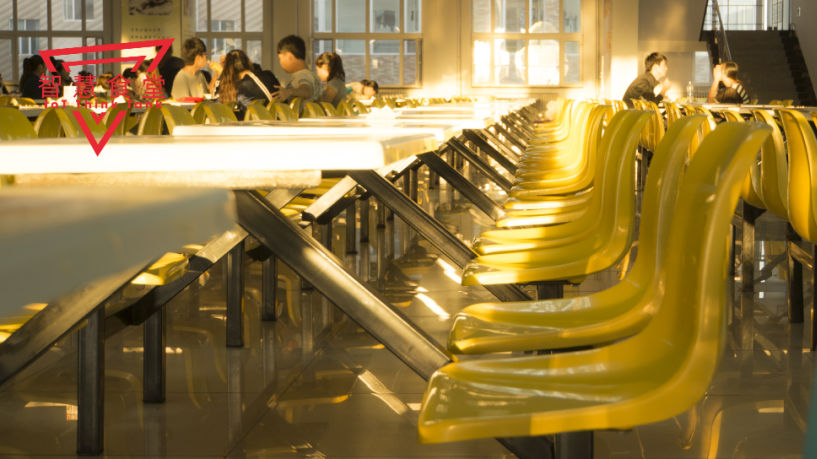
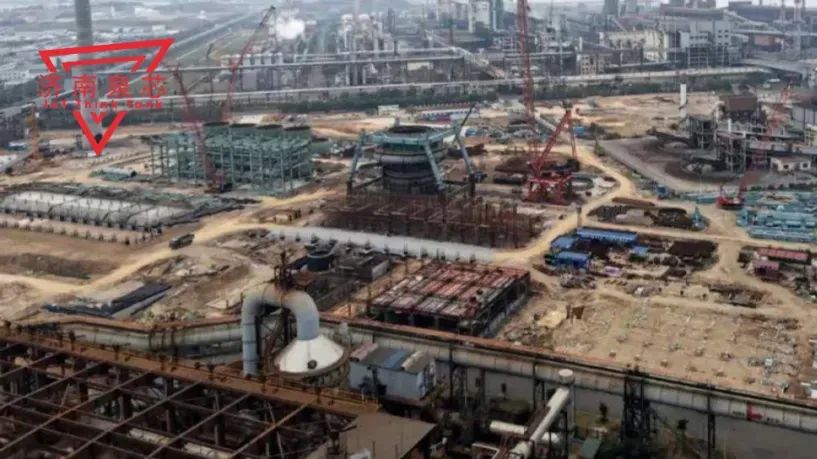